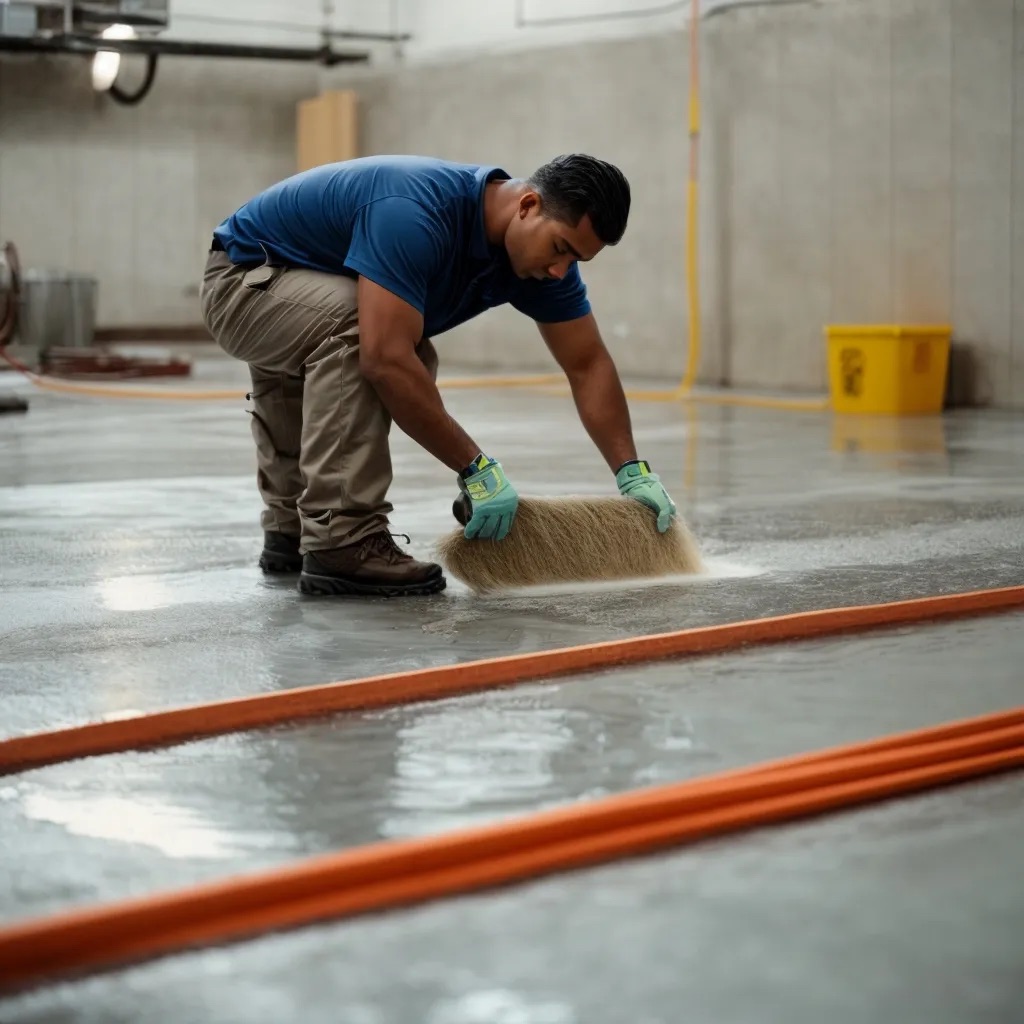
Concrete coatings serve as a protective barrier for various surfaces, shielding them from a range of damaging factors such as moisture, chemicals, abrasion, and weathering. They are essential for preserving the integrity and aesthetics of concrete structures, whether indoors or outdoors.
This article is designed to be a comprehensive resource for individuals seeking guidance on applying concrete coatings effectively. By providing detailed step-by-step instructions and valuable tips, we aim to empower readers to achieve professional-quality results and ensure the long-term durability of their coatings.
Concrete coatings offer a multitude of benefits, including enhanced durability, improved appearance, and increased resistance to stains, chemicals, and UV rays. By investing in concrete coatings, property owners can prolong the lifespan of their surfaces and reduce maintenance costs over time.
Preparing the Surface
Effective surface preparation is the foundation of successful coating application. It involves removing contaminants, repairing surface defects, and creating an optimal substrate for coating adhesion. Neglecting this crucial step can compromise the performance and longevity of the coating.
Surface preparation encompasses several key tasks, including cleaning, repairing cracks and spalling, and etching. Cleaning involves the removal of dirt, oil, grease, and other contaminants using appropriate cleaning agents and methods. Repairing cracks and spalling involves filling voids and repairing damaged areas to ensure a smooth, even surface. Etching enhances surface adhesion by creating a profile that allows the coating to bond effectively.
To achieve optimal results, it’s essential to follow best practices for each surface preparation task. This includes selecting the right cleaning agents and equipment, using high-quality repair materials, and ensuring thorough surface drying before proceeding with coating application.
Choosing the Right Coating
Choosing the right coating involves assessing factors such as environmental conditions, surface usage, and aesthetic preferences. It’s essential to select a coating that meets the specific requirements of the project, whether it’s decorative, protective, or functional in nature.
There is a wide range of concrete coatings available, each with unique properties and applications. Epoxy coatings offer excellent durability and chemical resistance, making them suitable for high-traffic areas. Polyurethane coatings provide superior UV resistance and are ideal for outdoor applications. Acrylic coatings offer versatility and ease of application, while polyaspartic coatings offer rapid curing times, making them suitable for time-sensitive projects.
When selecting a coating, factors such as durability, aesthetics, performance requirements, VOC compliance, and maintenance needs should be taken into account. Consulting with a coatings specialist or manufacturer representative can help ensure the chosen coating meets the project’s specific needs and performance expectations.
Gathering the Necessary Tools and Materials
Before beginning the coating application process, it’s essential to gather all the necessary tools and equipment. This may include brushes, rollers, sprayers, mixing tools, safety gear, and surface preparation equipment such as pressure washers or grinders.
In addition to tools and equipment, various materials are required for coating application, including primers, sealers, topcoats, and any additives or pigments necessary for the specific coating system. Choosing high-quality materials from reputable manufacturers is crucial for achieving optimal results.
Investing in high-quality tools and materials is essential for achieving professional-quality results. It’s important to choose products that are compatible with the chosen coating system and follow the manufacturer’s recommendations for application and compatibility.
Mixing and Dilution
Proper mixing and dilution are critical for achieving a uniform coating and optimal performance. Following the manufacturer’s guidelines for mixing ratios and dilution ensures consistency and reliability in the application process.
Thoroughly mixing components and avoiding overmixing are essential for achieving a homogeneous mixture. Testing the mixture’s consistency regularly and making adjustments as needed helps ensure uniformity throughout the application process.
Adjusting the mixture to achieve the desired viscosity and coverage is necessary for optimal application. Adding small amounts of solvent or water to thin the mixture or additional coating material to thicken it allows for customization based on specific project requirements.
Application Techniques
Following the manufacturer’s guidelines for coating application is crucial for achieving optimal results. This includes priming the surface if necessary and applying the coating using the appropriate method, whether it’s rolling, brushing, or spraying.
Achieving a smooth and even application requires proper technique and attention to detail. Using steady, overlapping strokes and avoiding overworking the coating helps ensure consistent coverage and appearance.
Selecting the appropriate application method based on the coating type, surface area, and desired finish is essential for achieving the desired results. Practicing proper technique and making adjustments as needed during the application process ensures optimal coverage and adhesion.
Working in Sections
Working in small sections allows for better control and consistency throughout the application process. It also helps maintain a wet edge, preventing lap marks and ensuring a uniform finish.
Working quickly and efficiently, applying the coating in small, manageable sections, prevents the coating from drying between sections and ensures consistent coverage.
Feathering the edges between sections and avoiding stopping midway through a section helps prevent visible seams or lines and ensures a cohesive finish.
Drying and Curing
Proper drying and curing are essential for achieving the desired performance and durability of the coating. Rushing the curing process can result in premature failure or inadequate film formation.
Monitoring visual cues such as color change, tackiness, and film formation helps assess drying and curing progress. Using moisture meters or other testing equipment ensures compatibility with the coating and substrate conditions.
Protecting the coated surface from foot traffic, vehicle traffic, moisture, and other sources of damage during the curing process is essential for ensuring long-term durability and performance.
Post-Application Inspection and Touch-Ups
Conducting a thorough inspection of the coated surface allows for the identification of any imperfections or defects that may require touch-ups or repairs.
Promptly addressing any touch-ups or repairs ensures the integrity and appearance of the coating. Using appropriate patching materials and techniques for minor imperfections and consulting with a coatings specialist for more significant defects ensures satisfactory results.
Performing a final inspection with the client or project stakeholders ensures that all touch-ups and repairs have been satisfactorily addressed. Obtaining written approval or sign-off confirms the successful completion of the project and client satisfaction.
The application of concrete coatings requires careful planning, preparation, and execution. By following the step-by-step guide provided in this article, readers can achieve professional-quality results and maximize the longevity of their coatings.
Encouraging readers to follow the comprehensive guidance provided in this article empowers them to execute successful coating projects with confidence. By investing in proper techniques and materials, anyone can achieve professional-quality results and enjoy the benefits of durable, aesthetically pleasing concrete surfaces.
Highlighting the importance of attention to detail, patience, and adherence to proper procedures, the closing remarks emphasize the satisfaction and pride that come with achieving professional-quality results in concrete coating application. By following the detailed guidance provided in this article, readers can elevate their coating projects and enjoy long-lasting, visually appealing results.